Techniques
The techniques
Murano glass is renowned worldwide for its beauty, quality, and variety of colors and styles.
Behind every extraordinary piece of Murano glass lies a series of craftsmanship techniques passed down from generation to generation. We have chosen to highlight some of the most commonly used techniques in our furnace to share a glimpse of the work we do and our primary mission: to preserve and pass on the richness of our artistic and artisanal heritage.
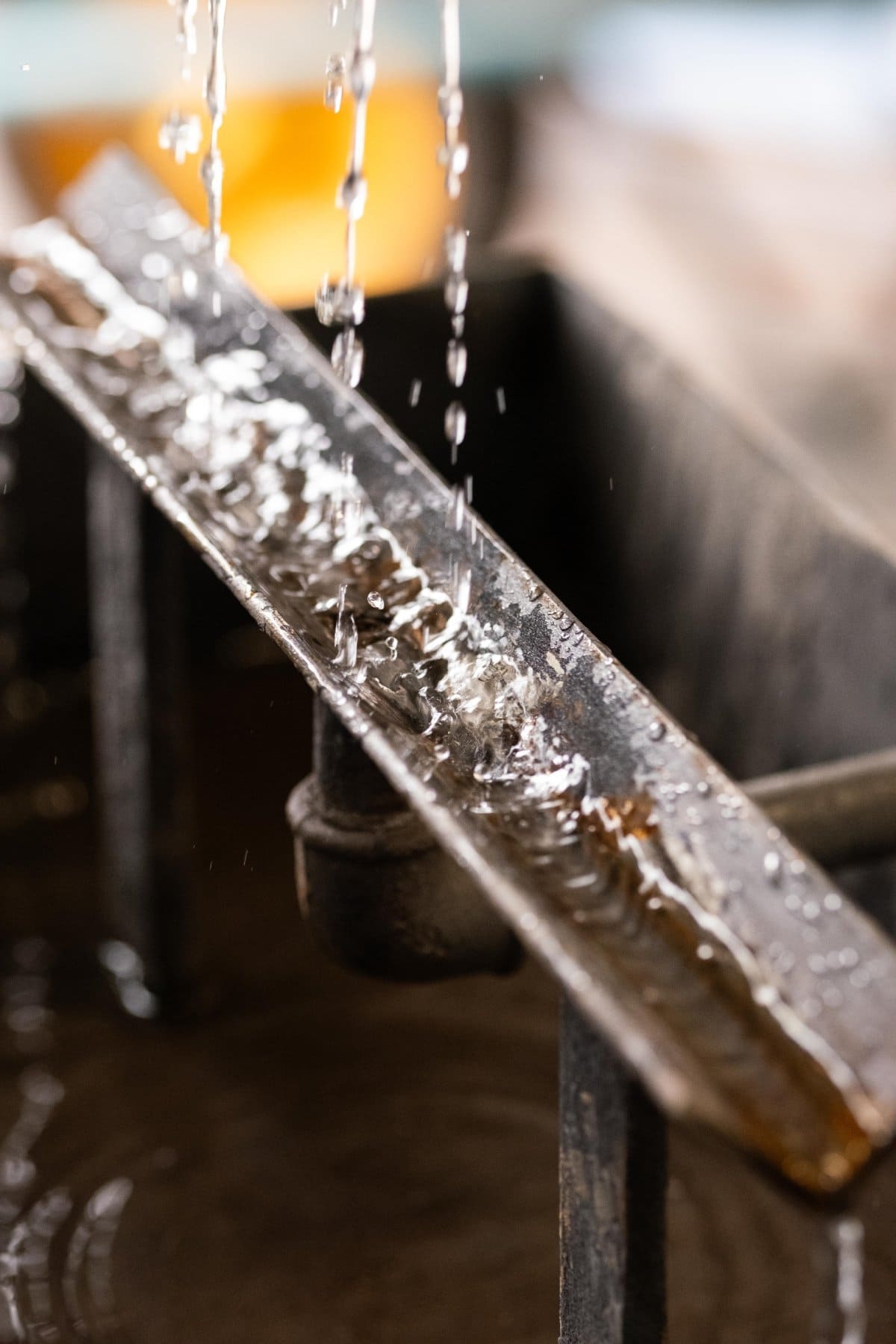
Blowing
This is one of the oldest and most iconic techniques used to create Murano glass. Molten glass is blown through a long metal tube to shape the desired object. Master glassmakers skillfully manipulate the molten glass using specialized tools to create form and texture, resulting in unique chandeliers, vases, glasses, and other art pieces. The air blown into the pipe inflates the glowing mass of glass, which then takes shape under the expert hands of the master. The temperatures, as in the entire furnace, are extremely high, and the glass must be worked quickly to maintain its malleability.
Murrine
This is an ancient glassmaking art that, as the name suggests, originates from Murano. It involves creating intricate glass decorations using colored glass rods. The process begins by melting glass in different colors to form a compact cylinder, which is then pulled and stretched into a thin rod. These rods are cut into small segments, called murrine, which reveal a complex design within. The murrine can be arranged on a surface of molten glass and then reheated and fused together, creating extraordinary patterns. This technique requires great precision, as each step must be carefully executed to preserve the clarity of the designs.
Grinding
This technique involves shaping and refining the surfaces of glass objects using abrasive tools. The process usually begins with the creation of a rough glass object, which may be blown, cast, or otherwise formed. Once the desired shape is achieved, the object undergoes grinding. By passing the object against abrasive discs, the glass is gently removed, allowing for smooth surfaces, precise angles, and intricate details. Grinding can be used to correct imperfections, create flat or curved surfaces, and add decorations such as engravings and carvings.
Filigree
This process begins with the creation of glass threads, which are formed by pulling molten glass into thin filaments. These threads, often in various colors, are then intertwined, arranged, or wrapped together to create intricate and delicate patterns. Once the threads are prepared, the artisan arranges them on a surface of molten glass or within a still-soft mass of glass. Using special tools, the threads are carefully positioned to form the desired design. The entire piece is then reheated in the furnace to fuse the glass threads with the main structure, ensuring that the design is stable and enduring. Filigree allows for the creation of extraordinary visual effects, with patterns that appear to float within the glass.
Chalcedony
This is a refined technique that mimics the appearance of the semi-precious stone chalcedony, characterized by a complex blend of colors and veining. Introduced in the 15th century, this technique involves melting various metallic oxides into molten glass, creating a wide range of tones and shades that resemble the natural patterns of the stone. The process begins with melting glass in a crucible, where oxides such as copper, iron, and manganese are added. During cooling, these oxides combine and separate, forming streaks and swirls of color that give the glass a unique marbled appearance. Each piece of chalcedony glass is one-of-a-kind, as the veining and shading vary unpredictably.
Incalmo
This technique involves joining two or more parts of glass of different colors into a single piece, creating sharp and precise transitions between various hues. The incalmo process begins with the creation of individual glass segments, each blown and shaped separately until the desired form is achieved. Each segment is then heated until it becomes malleable, and the ends are carefully joined and fused together while the glass is still hot. Once the segments are joined, the different sections of glass are reheated and worked to achieve the final shape. The artisan's skill lies in maintaining the precision of the junction lines, creating a visual effect of clear contrast and continuity between the colors.
Gold Leaf
This technique involves applying very thin layers of gold onto glass surfaces to create elegant and sparkling decorations. The process begins with blowing the glass, which is shaped into the desired form while still malleable. Once the initial shape is achieved, the artisan applies ultra-thin sheets of gold onto the surface of the hot glass. After placing the gold leaf, the glass is reheated to integrate the gold into its structure. This step is crucial as it allows the gold to adhere firmly to the glass without burning or losing its luster. The artisan can then continue to blow and shape the glass to achieve the final form, ensuring that the gold is evenly distributed and creates the desired decorative effect. In addition to gold leaf, there is also a variant using silver leaf.
Lampworking
This method allows for the creation of intricate details and complex shapes, making it ideal for producing beads, small sculptures, and other small decorative items. The process begins with the use of thin rods of colored glass, which are heated in the flame of a gas torch until they become soft and malleable. The artisan, with a steady hand and keen eye, manipulates the molten glass using various tools, such as tweezers, needles, and spatulas, to shape it into the desired form. Precision is essential, as the glass must be continuously rotated and worked to maintain a uniform shape and avoid imperfections. Lampworking allows for the addition of fine details and complex decorations.
Glass Paste
Also known as pâte de verre, is a refined technique that dates back to ancient Egypt and was later perfected by Murano glassmakers. The process begins with grinding glass into a very fine powder, which is then mixed with a binder to create a malleable paste that can be shaped into the desired form, such as the characteristic flowers found in Venetian chandeliers. Glass paste allows for a wide range of effects, from delicate translucency to vibrant and saturated colors, often enhanced with fine and intricate details.
Sommerso
This technique involves encapsulating layers of colored glass within a transparent outer layer of glass. This method creates an extraordinary three-dimensional effect, with the internal colors appearing to float and move beneath the smooth and shiny surface of the glass. The process begins with blowing a core of colored glass, which is shaped into the desired form. This core is then dipped into a crucible containing molten transparent glass, fully encasing it. The artisan then further blows and shapes the piece, ensuring that the layers of glass fuse perfectly without trapping air bubbles or impurities. Among the most appreciated sommerso pieces are marine-themed sculptures, miniature aquariums that recreate incredible ecosystems.
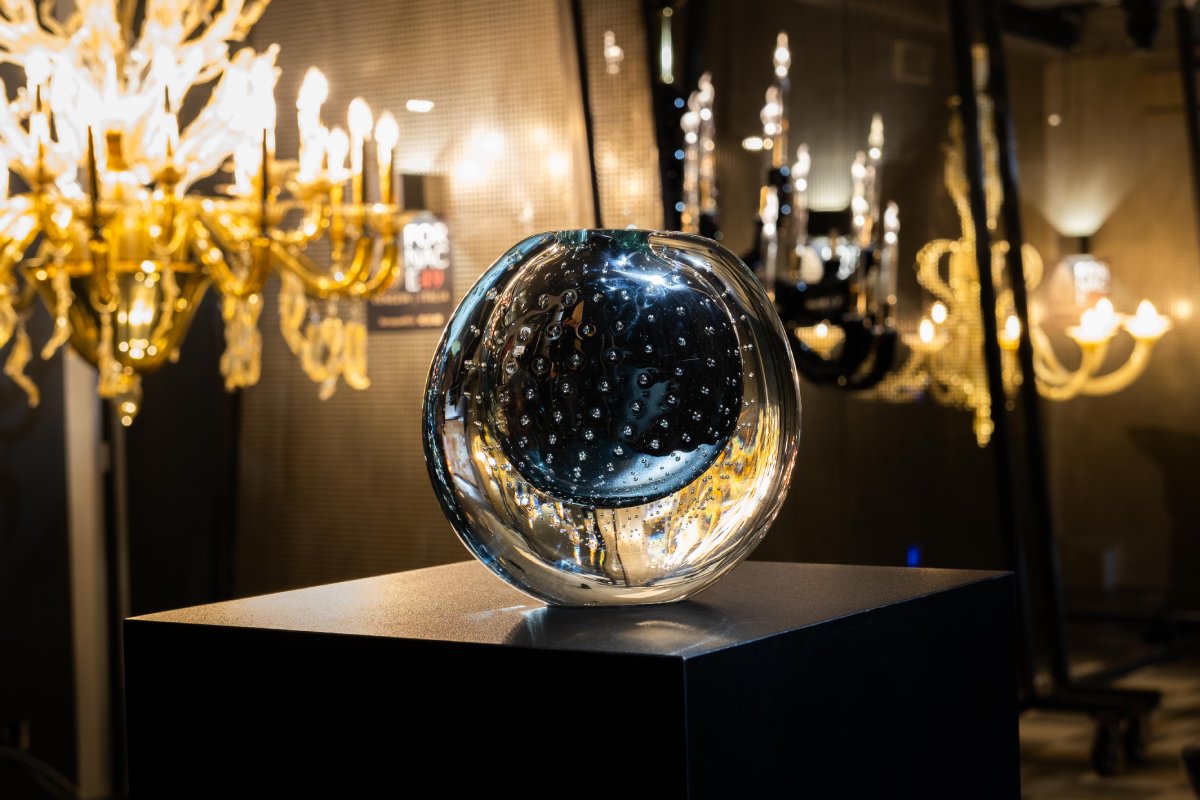
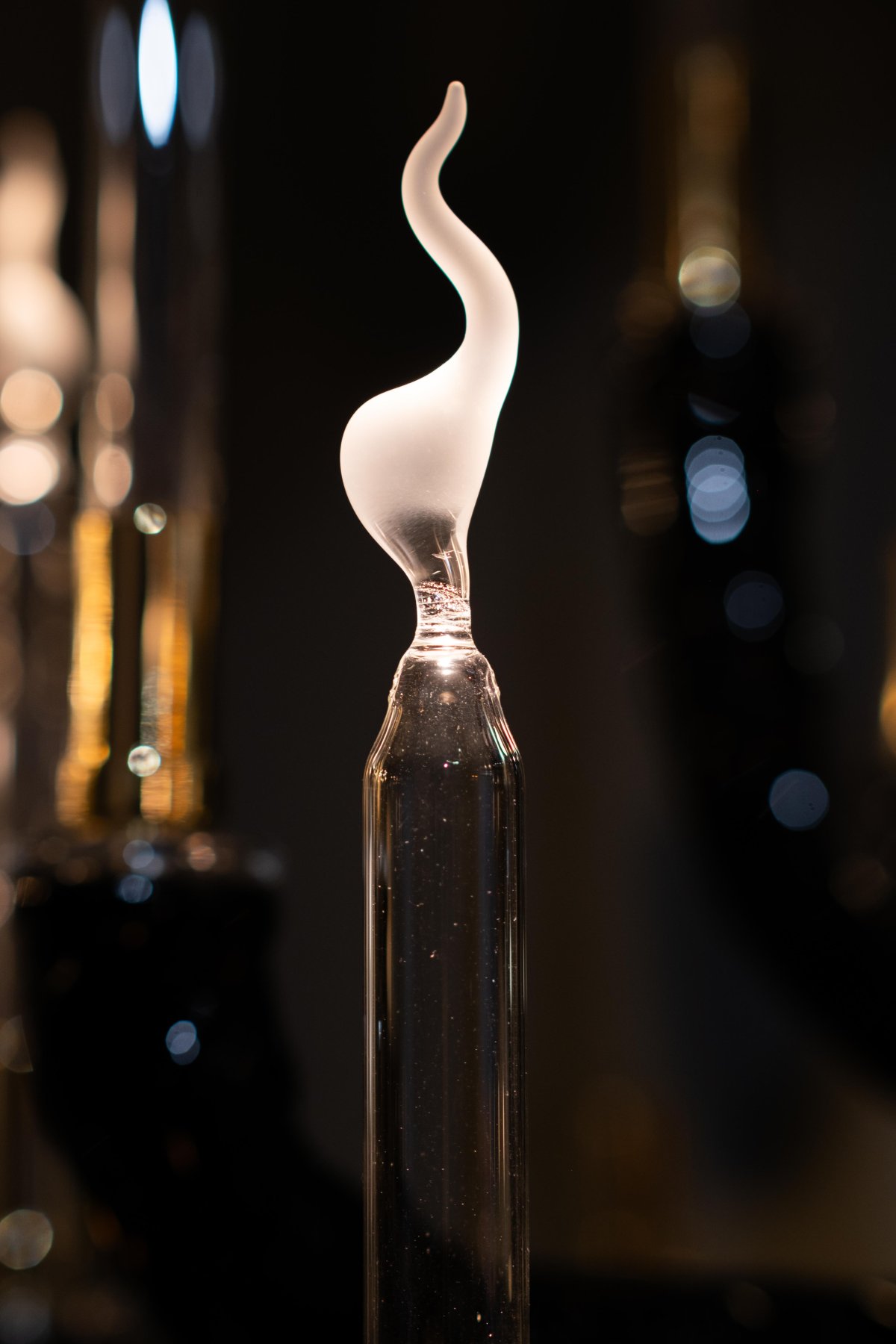
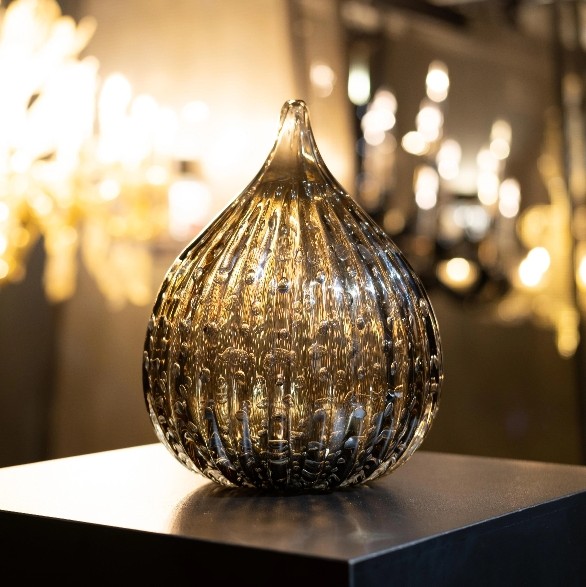
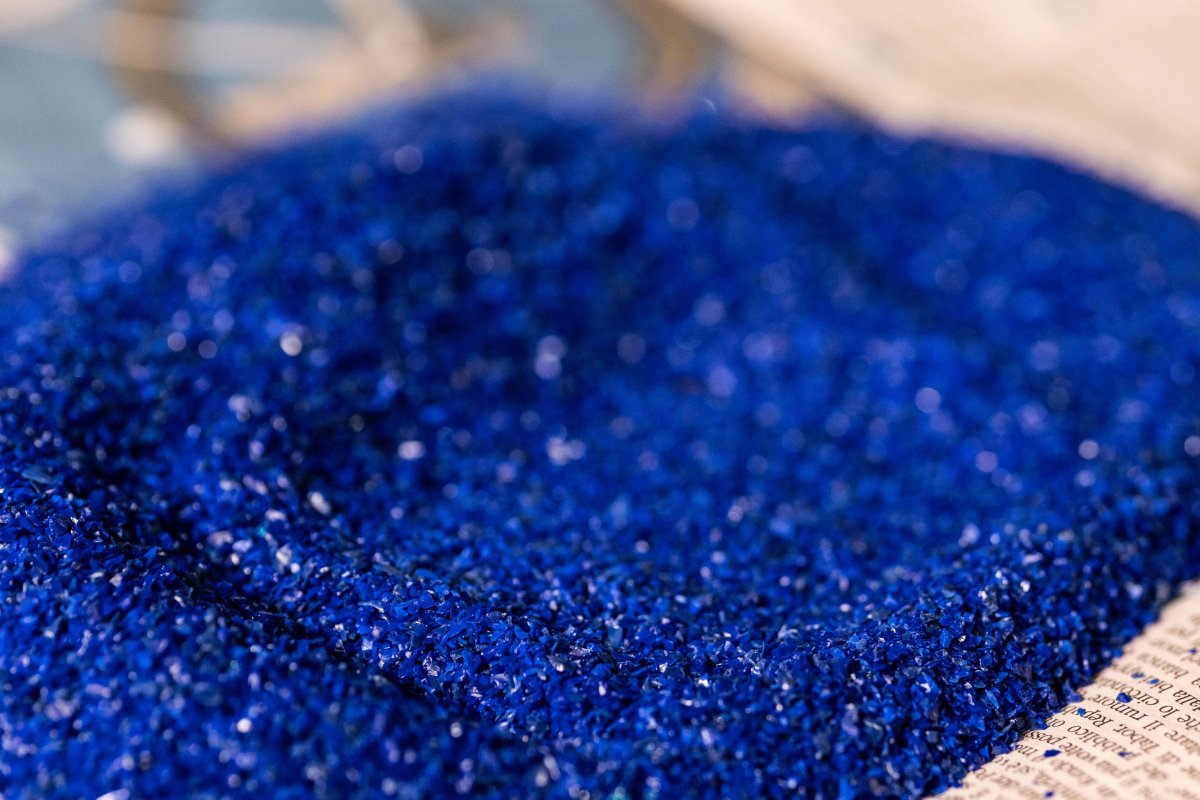
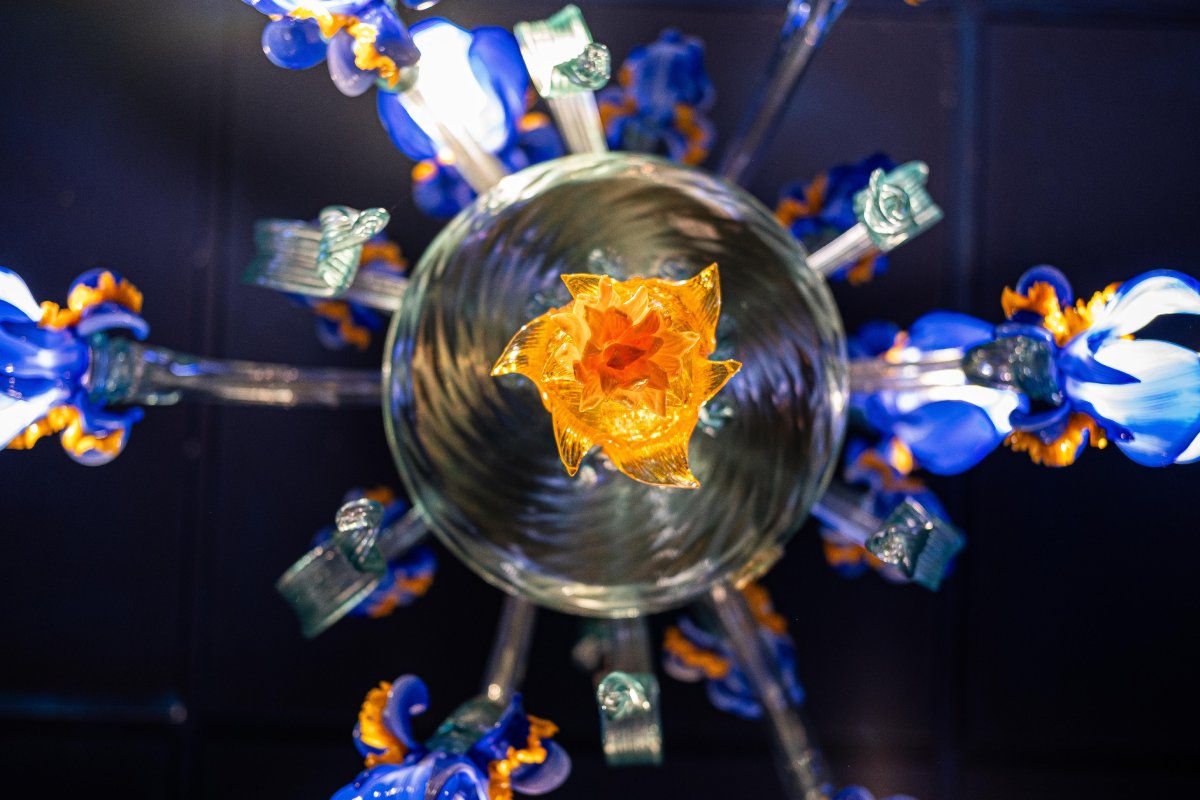
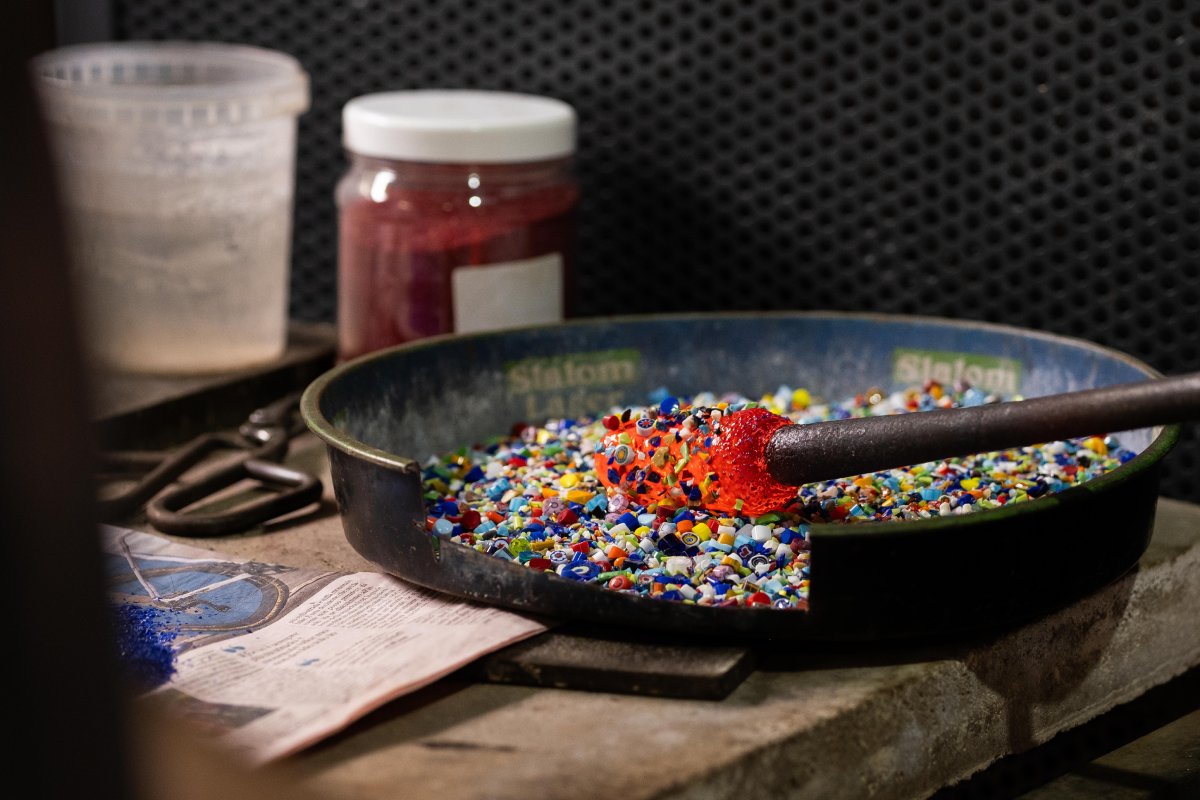